Exelys™ is an innovative and complete sludge reduction solution that works in continuous mode, combining thermal hydrolysis and anaerobic digestion.
Exelys™ is an innovative and complete sludge reduction solution that works in continuous mode, combining thermal hydrolysis and anaerobic digestion.
Overview
By coupling the thermal hydrolysis and the anaerobic digestion, Exelys™ offers better performance than a conventional digestion and optimizes sludge treatment by producing:
- 5 to 35% less dry matter
- 30 to 50% more biogas
- No odours
- A pasteurised digestate, for control over the sanitation hazards and safe agricultural reuse.
Exelys™ handles all kinds of organic, industrial or municipal sludge and can also handle grease.
Applications
Exelys™ is available under the 3 following configurations:
LYSIS/DIGESTION (LD) CONFIGURATION
Thermal hydrolysis is performed on the whole or a part if the sludge stream prior to digestion.
This configuration reduces digester volume by a factor of 2 to 3, reduces the amount of sludge and guarantees that it is sanitized while increasing biogas production.
Using the LD configuration, the throughput of an overloaded digestion plant can be doubled, thus avoiding the need to build additional digestion capacity.
DIGESTION/LYSIS (DL) CONFIGURATION
The hydrolysis reactor is installed on a sludge recirculation loop combined with a digester. Thermal hydrolysis is applied to part of the digested sludge.
This configuration gives the client wide flexibility whilst using a smaller scale hydrolysis stage.
Using the DL configuration, digestion capacity of an existing installation can be increased by up to 30%.
DIGESTION/LYSIS/DIGESTION (DLD) CONFIGURATION - PATENTED
Thermal hydrolysis is applied to all of the digested sludge from digester 1. Then the sludge is cooled and diluted before breakdown continues in digester 2.
This is the optimum formula in energy terms as it uses less steam while producing more biogas and electricity.
It also enables the greatest reduction in the amount of sludge to be produced.
Features & Benefits
Exelys™ works continuously 24 hour a day and has a simplified operation and maintenance, with a limited footprint.
This process allows:
- Reduced digester related investment for new installations
- Reduced operating costs:
o Less sludge to dispose
o At existing installations, the digestion capacity can be increased by handling new inputs.
- Income is generated from:
o Either processing external inputs through co-digestion
o Either selling the energy produced by co-generation or producing bio-methane
Exelys™ is a solution that guarantees energy and environmental performance, thanks to:
- Conversion into "green" electricity via co-generation
- Bio-methane production (for injection into the network or as fuel)
- Low steam consumption
- Reduced carbon footprint
- Many possibilities for using biogas: with external input (co-digestion), energy self-sufficiency or even a positive energy footprint may be achieved by the plant.
Exelys™ combines with other Veolia sludge treatment processes such as Athos™ (hydrothermal oxidation), Pyrofluid™ (incineration), BioCon™ (thermal drying), Solia™ (solar drying) and completes them to offer even more sustainable solutions.
Some references
- Billund, Denmark, 2016: 130,000 PE and 3,300t DS/year
Read more at http://billundbiorefinery.dk/en/
- Marquette-Lez-Lille, France, 2015: 620,000 PE and 22,000 t DS/year
Read more at http://www.veoliawatertechnologies.com/en/municipal-water-treatment-case-studies/wastewater/marquette-lez-lille-france
- Versailles, France, 2015: 330,000 PE and 8,300 t DS/year
"Carré de Réunion"
- Bonneuil-en-France, 2012: 15,000 PE and 300 t DS/year
Industrial prototype
Applications
Continuous thermal hydrolysis operating 24 hours a day with feed and removal levels that are adjustable in real time, Exelys™ operates under controlled temperature (165°C), pressure (9 bar) and duration time (approximately 30 minutes) conditions.
The system is controlled by a PLC that modulates the steam flow rate in line with the amount of sludge injected.
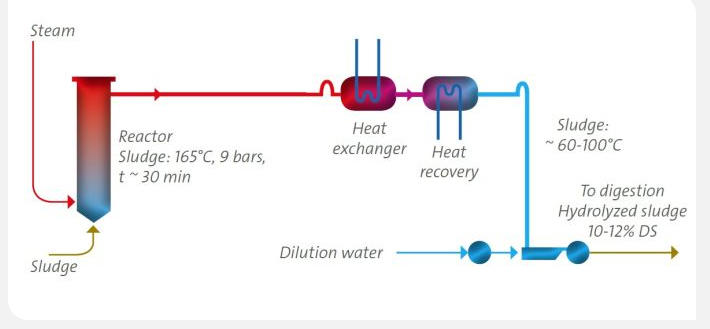