THE CLIENT
Food and beverage companies currently face several challenges with water management, which is especially true concerning ingredient water used in the actual product. It is a key challenge to monitor, in real-time, the quality of ingredient water ensuring the maximum traceability of production processes and to remain compliant with regulations.
THE PROJECT SCOPE
In September 2015, a 100m3/h water treatment plant for a global beverage leader was installed in North Africa. BERKEFELD PurBev®, a hygienic water treatment solution specifically for the food and beverage industry, was implemented. Additionally, our client was looking for a way to considerably improve the monitoring of their ingredient water and had an objective to improve the water consumption key performance indicator (KPI) liter-to-liter.
THE CHALLENGE
During operation the performance of two ultrafiltration units had severely and abruptly declined. Discussions, analysis and various countermeasures, such as CIP (clean-in-place) procedures on site, had been carried out without sustainably solving the problem. Since a further degradation of the ultrafiltration performance would have led to a plant shutdown — causing considerable damages and costs — an action plan was defined by our process experts.
The main objectives:
- Determine the root cause of the rapid differential pressure increase.
- Reduce the differential pressure of the ultrafiltration systems by performing modified CIP procedures.
- Inspect the dosing equipment and dosing rates.
- Check the chemical quality and concentration levels to meet stricter regulations.
THE ACTION
Hubgrade was implemented and so process experts were able to investigate the causes using available data and trends from the previous months’ and suggest counter actions in a timely manner. Hubgrade has successfully allowed the company to closely monitor their ingredient water in real-time by monitoring the parameters of PurBev, with secured access to this information anytime, anywhere and on any device.
CLIENT BENEFITS
Our client is now able to fully access real-time data on ingredient water processes and monitor the quality according to regulations and, more importantly, to their specifications. A team of Veolia Water Technologies’ experts were in charge of analyzing the reports generated from the key performance indicators and sending out immediate feedback in case of any future problems. These experts also provided recommendations and advice on how to improve operations.
The introduction of digital services means our client’s processes and plant are now, as a whole, more reliable. Thanks to Hubgrade the client was also able to reduce their operating costs.
This project has not only allowed for the client to benefit from increased reliability but also from increased plant uptime and an overall improvement in performance. The client’s feedback and testing has allowed us at Veolia Water Technologies to considerably improve our technologies, services and the PurBev design.
KEY FIGURES
- Increased membrane lifetime from eight to 12 months to two to five years.
- Reduced liter-to-litre key performance indicator from 3.0 to 1.8 litre.
- Prevented five to eight days downtime thereby avoiding production losses worth hundreds of thousands of euros and an emergency intervention
KEY FEATURES
- Remote monitoring of parameters.
- Remote control on demand, in close cooperation with the client.
- Operations reporting.
- Feedback on performance and recommendations for optimization.
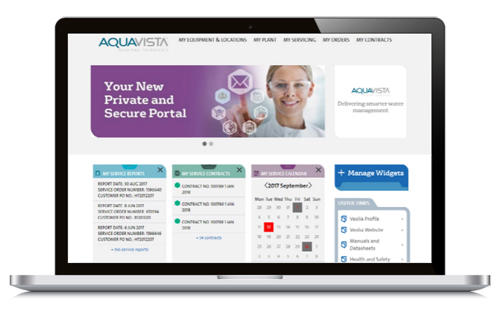
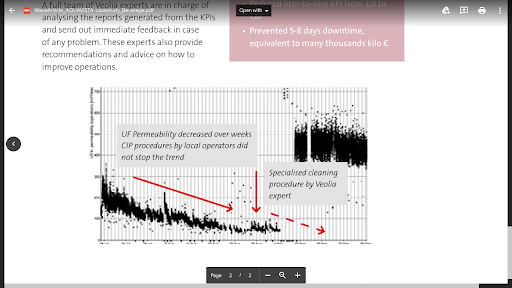